KNOWING THE RANGE. Exeter, Ontario, strip-tiller Mike Stran uses Ag Leader’s OptRx crop sensors installed on his high-clearance sprayer — with a Y-Drop system installed in 2013 — to apply late nitrogen on his corn.
There’s little doubt among farmers that data pouring from a myriad of displays, sensors, monitors and other precision farming equipment is going to help them be more efficient. However, analysis and timing often stand in the way of that goal.
To turn information into action, a farmer has to decode and process the mountain of gigabytes he’s pulled from his farm and assign meaning to it, so he can make appropriate and timely management decisions.
Crop-sensing technology is evolving to meet both those challenges. By no means a new technology, remote sensors, usually affixed to sprayers and sidedress machines, collect and immediately use real-time data — giving it’s user the ability to have tailored nitrogen (N) prescriptions for crops before it’s too late.
The Learning Curve
As with any precision equipment, picking up the idea of crop sensing and running with it can be tricky at first.
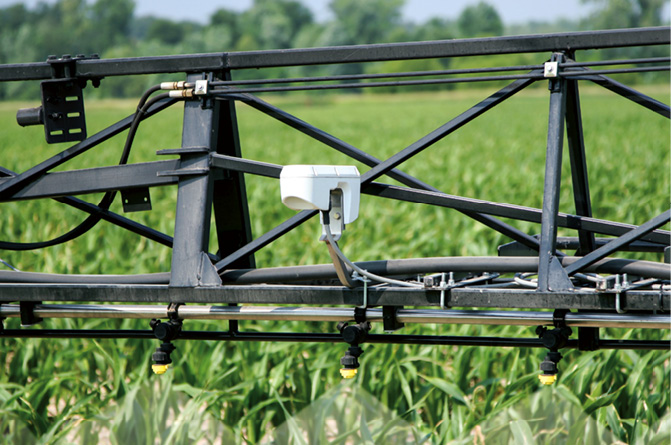
DATA ON TAP. Crop sensors have been evolving for the past decade to address farmers’ need to not only turn data into action, but do so in real-time. Remote sensors, usually affixed to sprayers and sidedress machines, collect and immediately use data — giving their user the ability to have tailored nitrogen prescriptions for crops before it’s too late.
Photo Courtesy of Trimble
Mike Strang, who strip-tills corn, soybeans and edible dry beans and no-tills winter wheat on 1,600 acres near Exeter, Ontario, says the Ag Leader OptRx crop sensors installed on his high-clearance sprayer — with a Y-Drop system installed in 2013 — is simple, but it’s not just plug-and-play.
This year was his first using crop sensors. He picked up the technology to apply fungicide and late N to his fields based on need. He says the best beginner’s advice he received was from a crop sensing roundtable discussion at the 2015 National No-Till Conference in Cincinnati.
“The guys in the group had OptRx sensors or GreenSeekers and the comment I took home was that you still need to have a good idea about the maximum and minimum amount of N you want to apply on the farm before you set your sensors,” says Strang. “We had to base this on how much N we usually put on. Ordinarily, we apply 100 pounds per acre of slow-release urea at planting. So, I knew I didn’t want to apply any more than another 100 pounds of 28% N during my late application, so I set that as my maximum.”
Strang also says experience with nitrate testing and variable-rate fertility applications made establishing parameters simpler.
“In the back of our heads we knew how little N we could go with in some places, and the most we would probably need. That helped us come up with a range of 15-100 pounds of N for our area and our yield goals,” he says.
Return on Investment
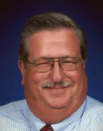
“With sensors, we’re able to fill in nitrogen where it’s needed to get the optimum yield and savings...” — Mike Shuter
The return on investment for crop sensors is often spoken of nebulously in the farm industry because it’s difficult to sort the results without side-by-side comparisons. Miami, Okla., no-tiller Brent Rendel, who’s been using the technology faithfully for a decade, says he was intent on proving the technology’s effectiveness to himself.
Rendel grows 4,000 acres of winter wheat, winter canola, corn, grain sorghum and soybeans and has been using Trimble’s GreenSeeker remote sensors on his high-clearance sprayer for late N applications. After many side-by-side comparisons, Rendel is confident saying that a crop-sensor system pays for itself at a much faster rate than farmers think.
He’s been exceptionally pleased with his system’s performance on his no-tilled winter wheat.
“I tell other farmers if they’re growing wheat without using some sort of a sensor to prescribe their N, they’re losing money,” Rendel says. “When I first started using sensors, I would do test strips across the field with my regular rate of N. Then I’d do the strips next to them with the GreenSeeker running.
“I didn’t have a yield monitor, so I when I’d go to harvest I actually went down the first strip then got a weight on it, then I’d harvest the adjacent strip and get a weight on that and compare the two.”
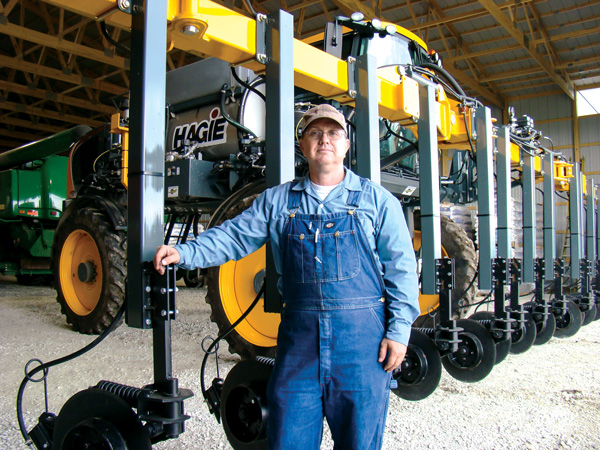
SEEING RETURN. Miami, Okla., no-tiller Brent Rendel has been using crop sensor technology for nearly a decade. His multiple side-by-side comparisons have shown him that he can expect to make $8-$15 per acre on winter wheat and $15-$20 per acre on corn. Sometimes that profit is in nitrogen savings, other times it’s in added grain production.
Rendel says the typical rule of thumb for winter wheat production in his area, as it pertains to N application, is 2 pounds of N for every bushel of yield goal.
“You may have some N from the previous year that you’ll have to credit, but you’re basically using your best estimate off soil testing,” says Rendel. “For my full rate, I would be topdressing 50-60 pounds of N, but on the strips with the GreenSeeker it was only putting on 15-20 pounds. There was a dramatic reduction in the amount of N it was prescribing that year.”
At weigh in, Rendel has consistently seen results that put the GreenSeeker ahead of his normal rate application, but not always in terms of yield.
“It’s not unusual for me to find that the full rate N strip had a higher yield, however, it has been very rare that extra yield pays for the N I had to put on to get it to that point,” Rendel says. “With the sensors on wheat, I can pretty much bank on $8-$15 of added profit per acre, depending on the price of N and grain in a given year. Sometimes that extra money is in the form of reduced fertilizer expense when you don’t need it, and sometimes that benefit comes from increased grain production in years when N uptake is favorable.”
Taking that a step further, Rendel has determined that on a good year, a sensor set-up can pay for itself running across only 2,000 acres.
“A system like mine on my sprayer will set you back $20,000 or $30,000,” he says. “With $5 wheat, people ask, ‘How in the world can you pay for that?’ But if I can generate an extra $10 per acre, which is a conservative estimate, I’ll only need about 2,000 acres to pay for a system.
“After that, the system will start paying me that $10 per acre. With corn, the ability to leverage in-season N is even greater than wheat. You’re looking at $15-$20 per acre.”
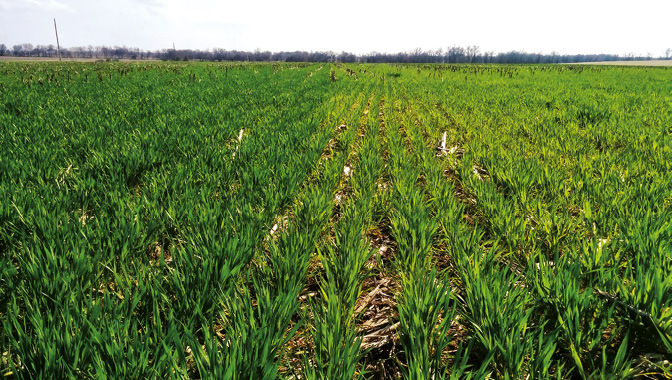
REFERENCE STRIPS. No-tiller Brent Rendel develops the maximum portion of his nitrogen (N) range to plug into his sensors by building up one particular zone in his field with as much N as it can take during pre-plant. In the no-tilled wheat above, the left side is Rendel’s N rich zone and the right is his standard rated field.
Rendel found this to be especially true last year when the GreenSeeker was prescribing a rate of 0 pounds of N for his corn on most passes. His sensors were telling him that there was little to no need for in-season N.
“In a normal year in my area, we grow 100 bushels of corn per acre,” he says. “Last year, we only applied 75 pounds of N per acre during pre-plant. It was following a normal crop, too.
“That year, we had 150 average bushels per acre of corn — some fields went to 180. Now why did it do that? I can’t tell you. If you look at the N cycle, between rainfall, residue decay, biologics, crop rotation, weather and everything else, it’s just so complex that guessing about rates and using rules of thumb just isn’t accurate enough.”
The way Rendel sees it, a farmer using anything less than real-time data from sensors to rate their fertilizer applications can only be right a third of the time. If a farmer doesn’t nail the rate on the head, he’s either using too much N or too little, which can be costly either way.
“I want to be right more often than I’m wrong,” he says. “Sensors aren’t perfect because you can’t always get out there at the exact right day at the exact right time. They’re probably only right about 70% of the time, but 70% right is a whole lot better than 33% right.”
Frankton, Ind., strip-tiller Mike Shuter installed OptRx sensors on his high-clearance sprayer, with a 60-foot N toolbar, for late N applications of 28%. He says the expense is justified because it helps fill in the N gaps left by his hog manure application.
Shuter has been using crop sensors for about 5 years on his 2,500 acres of corn. He purchased the sensors, originally, because the idea of applying N where his crop’s needs were the greatest fit well with his existing application methods.
“I tell other farmers if they’re growing wheat without using some sort of a sensor to prescribe their nitrogen, they’re losing money…”
“We use a lot of hog manure on our farms, and hog manure is pretty variable in terms of how much N is in it,” says Shuter. “It’s hard to know exactly how much N you got out of the manure. I think anytime you add late N you’ll see a benefit to your yield, whether you’re using sensors or not. But with sensors, we’re able to fill in N where it’s needed to get the optimum yield and savings.”
Sensor Weaknesses
Despite the benefits of the technology, Rendel has noticed two notable drawbacks. The first being that crop sensing for N application basically forces a farmer to split their N up, and second, that it’s imperative to use a late-application method.
“If you’re looking for a system that doesn’t need split applications of N, then sensors won’t work,” Rendel says. “By definition you have to split your N up with a late application. You always need to put some N up front to get the crop off and going, but you’re going to have to apply N in late season as well.”
To farmers already using a system like this, that’s not a concern. But a late application requires additional equipment, like a high-clearance machine, and it may push the farmer into an application timeframe that they find uncomfortable.
“With sensors, a farmer needs to apply N quite a bit later than they’re normally comfortable with,” Rendel says. “Around here, we typically topdress our wheat with a winter shot of N in January or February, when it’s frozen. With my wheat, we need 80 growth days before our late application, so that’s a full month after most guys around here have already topdressed.”
As an example, Rendel recounts a year when he had to fly on a few pounds of N per acre with a plane because wet weather kept him out of the fields.
“I knew I needed the N, but I just couldn’t get across the field in the ground rig, so I flew on a shot of N that extended me 2 more weeks, to the point where I could get back out in the field,” he says.
Rendel admits that at times, it may be even more nerve wracking with corn if weather isn’t cooperating. Normally, he waits until between V7 and V8 to sidedress his late application of N. At this point, the corn is growing fast and the opportunity comes and goes rather quickly.
“Unless you have a high-clearance sidedressing rig, it’s very hard to time your N application on corn,” Rendel says. “I have sidedressed tasseled corn before because that was the earliest I could get in on after V7. I did take a yield hit that year.
“On the risk-reward scale, though, I think the risk of not being able to apply N at the right time is worth the benefit sensors give you with not having to guess how much to apply.”
Crop Sensing’s Future
According to experts at both Trimble and Ag Leader, the demand for their crop-sensing products has continued to trend upward year after year and doesn’t show any sign of slowing down.
However, they have their own take on the future of the technology.
“We did release our handheld sensor option in 2012, but one of the interesting things about GreenSeeker is the improvements we’ve made really using the same hardware,” says Trimble marketing manager, T.J. Schulte. “Where we’ve seen big changes and will continue to see even bigger ones are in the algorithms we use to make calculations off the data GreenSeeker collects. The ways in which the technology has been evolving is in the quality and quantity of algorithms specific to areas of the country and crop types.”
Chad Huedepohl, Ag Leader’s sales manager for western North America, sees a heavy trend toward aerial imagery — specifically UAV imagery being used to assess and write prescriptions for crop health.
However, he sees that active sensors on the ground still have the advantage of cutting out a data processing stage that would normally have to be performed when working with UAV data.
“Active sensors on a sprayer are just running while you’re going through the field, so it assesses the data and implements the prescription in one step,” says Huedepohl. “I think seeing the technology used for more crop types, and different uses beyond N management, is in the short-term future.”
Strang agrees with Huedepohl. In fact, this year, in addition to applying late N, he used crop sensing and variable-rate technology to apply fungicide on his edible beans.
“It took a little bit of playing around, but I was able to adjust the rates,” Strang says. “I actually had less white mold pressure than I did in previous years.
“Obviously with white mold, a lot of it is environmental, but I can give credit to variable-rating fungicide with the sensors. I’m pretty sure somebody could figure out how to variable rate herbicide with sensors as well. There’s a lot of possibilities for other applications, not just for N management.”
Rendel also sees sensor trends bending toward UAVs, but where that industry currently falls short is in the hardware department, he says.
“With crop sensing, I think UAVs are the direction most farmers are hoping it goes,” says Rendel. “But there’s misinformation being touted about UAVs. There are some companies who are using converted Cannon cameras and just adding UV-filtered lenses to get an infrared-range image.
“That just isn’t the same thing as the normalized difference vegetation index (NDVI) data that crop sensors collect. NDVIs are mathematical formulas rather than just pictures.”
However, he feels that UAV-sensor platforms are inevitable, and researchers and manufacturers just have to connect the dots and package the computing power appropriately.
“I actually think, that within the next 5 years we’re going to have UAVs capable of imaging true NDVI,” Rendel says. “The technology already exists — it’s just a matter of getting all the computing power together. The UAVs will have to fly low and gather a lot of detail, so it’ll probably be something like a swarm of quad copters. I think it’s inevitable that remote sensing will move off the sprayer and onto a flying platform.”
Post a comment
Report Abusive Comment